Planning Maintenance Work with SAP
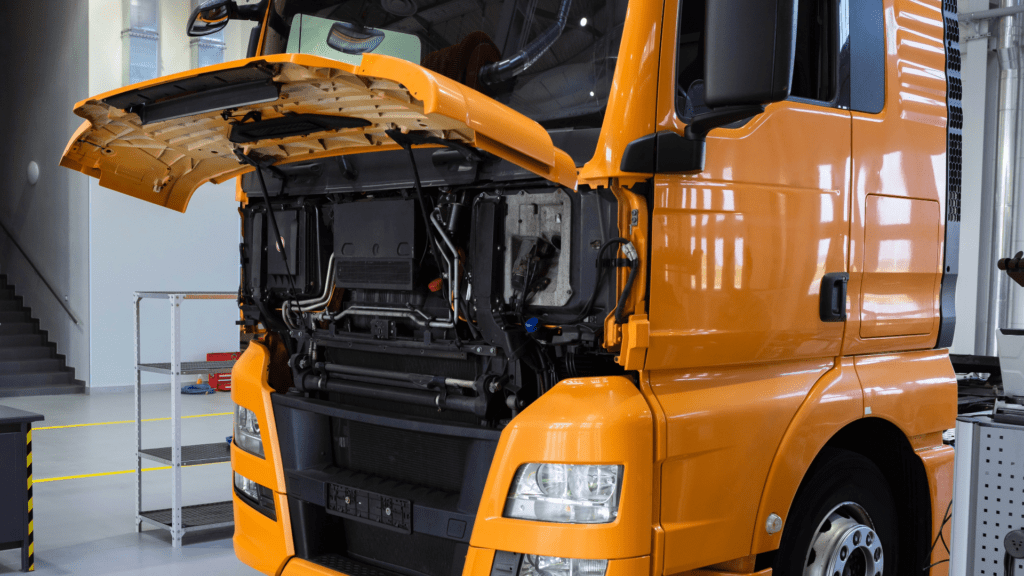
Regardless of what CMMS you might have in front of you, the trick to being a successful maintenance planner is for you to have a plan for every working day of the work and manage every minute of that day effectively. Time management is essential for a maintenance planner and is possible via self discipline and using every tool at your disposal to make sure you apply the right amount of effort on the right days of the week.
You’ll soon realize how the above preamble is important once I start explaining a typical Monday to Friday week for a maintenance planner. I’ll make three assumptions in the article, the first one is that your department will employ a full time scheduler; all completed work orders are reviewed by the supervisors and that your department plans and schedules work at least 3 weeks out from the current week.
A Maintenance Planner applies the ‘What’ and ‘How’ details to work they are responsible for. When the Planner has completed the planning effort on each work order, the status coding is updated. The output of the Maintenance Planner is the input for the Scheduler.
The Scheduler applies the ‘Who’ and ‘When’ details to work orders completed by the Maintenance Planner (Fully Planned Work Orders). When the Scheduler has completed their efforts, a scheduling meeting is held and an approved list of scheduled work orders is the output of this process. The output of the scheduling process is the input for the Maintenance Supervisor.
The Maintenance Supervisor executes the approved Scheduled Work Orders and provides constructive feedback to the Scheduler and Maintenance Planner on instances where problems were encountered.
Where re-planning of problematic work orders is required, the Supervisor will review comments from the tradesperson and approve the changes that need to be made. The completed work efforts of the Maintenance Execution Team are reviewed for compliance to the schedule and other criteria. The Reliability Engineer analyses the outputs of the Maintenance Execution Team to identify opportunities for improvement.
I’ll try not to make this article too SAP transaction specific in hope of still being able to provide some assistance to new Maintenance Planners that might be using other very good products such as Oracle, Maximo, Pulse, Pronto or Ellipse.
What work does a SAP Maintenance Planner process?
All assets (Functional Locations/Equipment) of your company will all be assigned a ‘Planner Group’ as part of Master Data creation process. As notifications (work requests) and work orders are created for assets, the planner group can be filtered on all search selection queries and the resultant list/edit transactions and the Maintenance Planner will process work that relates to one or more planner groups that are assigned to them.
The Maintenance Planners workload will consist of:
1. PM01 Maintenance Strategy Work
2. PM02 Corrective Maintenance Work (work arising from defects/requests for work). Your role is to apply maximum planning effort to each operation/activity on every work order.
3. Creating Corrective Maintenance Task Lists. If a work order is planned from scratch and there is the potential to do this job again multiple times in the future, then the Maintenance Planner creates a PM02 Task List/Standard Job.
4. Re-Planning of PM02 work orders (although undesirable as it means we failed the first time around).
5. Contribute to Budget Development. Maintenance Planners will become very knowledgeable of the assets they plan work for over time and as such it is only natural that they will be called upon to contribute towards development of the Maintenance Budget.
6. A Maintenance Planner may also become involved with long term PM03 Breakdown Work Orders to help out the Supervisors.
7. The Planner converts the backlog into a forward log.
The Maintenance Strategy, which is typically your PM01 work orders. These work orders are system generated via the inherent criteria. There should not be a lot of effort required in processing Maintenance Strategy Work orders, the underpinning task lists of these maintenance plans should have included, all scope and other documentation, parts, trade types and requirements etc. In a perfect world situation, all the Maintenance Planner should be doing with these work orders is just checking that they are fully planned and change the statuses of the work order/operation so that the Scheduler can view it on their work list. Obviously, if the Maintenance Planner needs to apply planning effort to a Maintenance Strategy PM01 work order, then the task list will need to be updated for next time, you don’t want to be doing this every time. Depending on your department, the Maintenance Planners may make these changes or a request to get the task list updated will need to be sent to the Reliability Engineer or Master Data Specialist, be sure to quote the work order number you tidied up on this occasion, go to the planning tab of the work order and quote the Maintenance Plan, Item and Task List details.
Corrective Maintenance, which, depending on your department may be:
1. Processed from a list of approved maintenance notifications coded with their Planner Group. In this situation, the Maintenance Planner will make work orders from approved notifications they feel they can work with. For notifications that don’t have enough detail or are duplication of existing work orders, these will be processed according to your department procedures.
2. Processed from a list of newly created work orders coded with their Planner Group. In this situation, the approved notification may have been made into a work order via a dedicated resource in your department; this would typically be a person with a good understanding of the assets and work planning requirements.
Creating Corrective Maintenance Task Lists is where the Planner opts not to reinvent the wheel every week. There will be very few work orders a Maintenance Planner will apply planning effort to whereby there is zero chance of this work needing to be done in the next 12 to 24 months. Especially if the work was created with a reasonably complex recipe, it is silly to waste all that effort. When you use all of the work order information to make a corrective maintenance task list/standard job, the next time that notification/work request is approved and on your list, you can ‘draw in’ the task list you created for this work last time and ‘Bingo’ everything you need is there for you. Change the status of the work order and operations to ‘planned’ and then move on to the next job.
Re-Planning of PM02 Work is necessary when the Maintenance Execution Team were unable to complete work due to problems that should have been detected in the planning process. This could relate to incorrect scope, parts or resources assigned, typically, if the maintainers could have come up with a work around solution to get still this work completed, regardless of any mistakes, they would have but when that’s not possible, the work needs to be re-planned. Be sure to check if any re-planned pm02 work orders resulted from a task list, if they do, obviously, you will need to go into the task list and make the necessary changes.
A Maintenance Planners contribution to the Maintenance Budget is highly important. A lot of the Maintenance Planners work is somewhat repetitive and certain types of equipment tend to have certain types of problems and the Maintenance Planner’s effectiveness is often measured by the accuracy of the cost estimate applied to the work order prior to it being released. With all this in mind, the Planner does become very in tune with how much things cost and assuming the department manager is able to provide them with a budget development software product that is straight forward to use and doesn’t waste peoples time too much, then the Maintenance Planner will be able to go through and offer/make adjustments as required.
Some equipment breakdowns cannot be fixed as quickly as the production team would like. This could be due to parts unavailability, manufacturing delays, specialist resources from overseas being required or in some cases a manufacturer may have closed their doors and no longer exists. Whatever the reason, you may have a tier 1 Asset not available for use for a considerable time. Resolving these issues will often be a ‘group effort’ and all stakeholders will do what they can to assist resolution. There will also be opportunities for other work to be performed on these assets whilst they are off-line and the planner will get involved with these. Time based Maintenance Strategies/Plans might need to be put on hold during these situations but this is strictly a decision that will be made by the Engineer, Superintendent or Manager.
A week in the life of a SAP Maintenance Planner.
It’s pretty hard to suggest one size fits all with how a Maintenance Planner should apply themselves to each day of their working week but I’ll have a go.
Before I go into details, it’s important for any new Maintenance Planner out there to understand, their role is not plan a fix for everything in the plant or on a machine over the next 5 days. All equipment will have defects but not all of them need to be fixed in the next scheduling period. The work reviewers should be assigning priorities based on a risk assessment process in a perfect world; otherwise they would be using their vast experience to assign the most appropriate priority to each job.
Even if all of the work orders with your planner group code assigned have the correct priority, you will still come across some weeks where there is an impractically large amount of work orders sitting in the system and with appearance that they need to be executed in the next period. You will need to work out which of these work orders can be ‘pushed forward’ into future schedule periods. For this, you will always need to display system status and user status in each work order/operation list/edit screen. This is where you will see that jobs are waiting on parts, waiting for scope development, waiting on information from suppliers etc, so unless you are certain that these jobs need to stay in that period, you will need to move them out into the future based on what you learn about each work order.
The other thing you need to check for is uncompleted work orders that now have a ‘planned date’ that is less than today’s date. Unless you have recently been successful with creating a working time machine, the maintenance execution team will most likely be unable to go back in time to those dates and do the work.
This is where the Maintenance Planner converts the backlog into a forward log.
Take the time to check each work order before changing the date, it’s possible that this task may have already been completed under the banner of another job, it may no longer be required or the scope requirements have changed and you will need to apply additional planning effort.
There would normally be planning cycle milestones to be completed each week. These milestones will be specific to the way your business initiates, plans, schedules, executes and completes work. For instance, not all Maintenance Planners need to spend a lot of time chasing down parts; this effort may be done by a supporting role in the organization. So there won’t be a day of the week where you need to make sure you’ve completed these efforts, instead you’ll have a day of the week whereby if the work order does not show that all parts required are here, it might simply get pushed to the next period for you to plan.
Assigning the trade types and the number thereof by the right day of a week will be critical for the scheduler. So you will need to have a day/time whereby you’ve gone through all of the work orders you are planning and if there are instances where certain resources will not be available to assist with a particular work order during the period you desire, then again, push that work order out to when it can actually happen. There is no value having a work order date positioned at a point in time where there is zero chance it could be done in full, on time and at specification.
Get all of your work order date changes done as soon as possible at the start of the planning week. This way, the only work orders you’ll be looking at in your list/edit screen are the ones you need to fully plan. Things will ‘pop up’ during each periods planning and these ‘break in’ jobs will take priority in most cases, so make sure you get all of the ‘housekeeping’ done as quickly as possible.
Wrapping this up with a few last comments.
If you are just now starting out as a Maintenance Planner, the first thing I would be getting help with is your role based ‘Weekly Plan’. One of the senior planners in the group should be able to assist you with this, if not your direct supervisor might even have one stored in SharePoint for you. Don’t let people waste your time, if you are caught in a conversation that is taking too long, whether it’s someone near you or someone you are on the phone with, stand up. Just the simple action of standing up will make you want to move on from that conversation. It’s possible that you were just too comfortable and have allowed yourself to get drawn into talking about something that is non-productive. I very rarely come across a Maintenance Planner that’s not at least a little stressed out about their workload. As I mentioned in the introduction time management is critical for a planner.
Don’t let some work orders consume too much time, do search online for ‘The 80/20 rule’. This will explain to you that we get 80% of the work done in the first 20% of the time. The waste happens when we spend 80% of our time trying to be perfect on the last 20% of the job.
In the ‘First Pass’ of your planning efforts for the upcoming period, go through all valid work orders and get them all to 80% planned first. Then re-look at that list and then work out what your approach will be to go through and get them all to a ‘fully planned’ status. If you’d like a look at what I feel a fully planned work order looks like, here is an article I published on my Blog Page about this subject a while ago.
I welcome your feedback.
If there is an article you’d like me to publish on my Blog for you, please leave a comment below.