Asset Lifecycle techniques to get the most out of your assets.
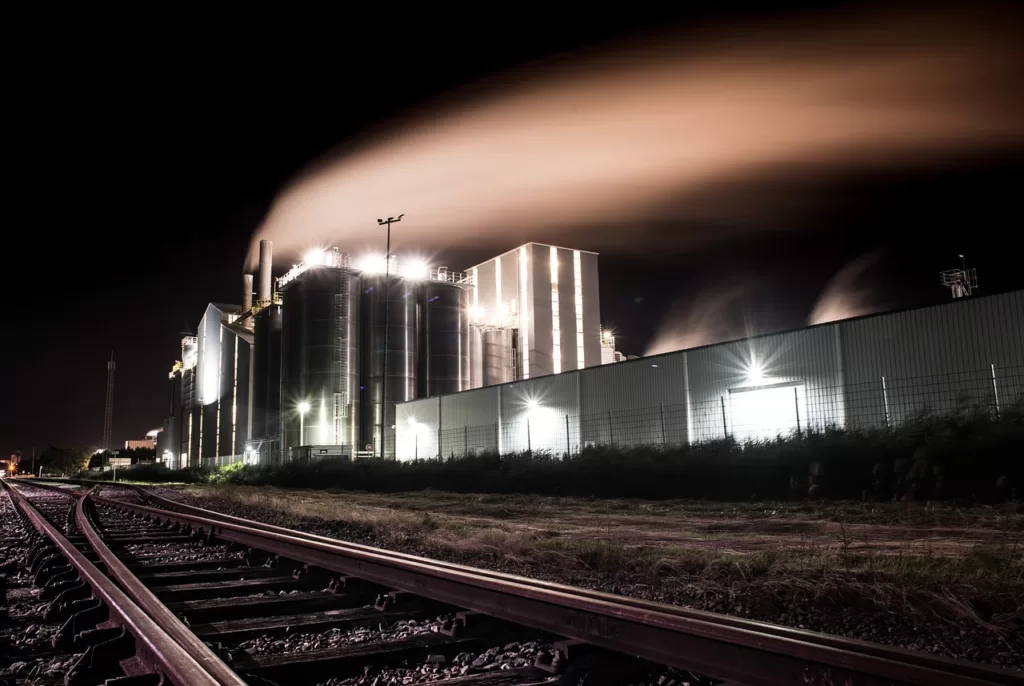
Getting the most from your assets in terms of lifespan, availability, reliability and performance without it costing you too much are naturally highly important goals.
These goals can be achieved via a number of different asset lifecycle techniques and our world often needs particular companies to do extremely well in this area, such as the ones that deliver electricity to our homes and hospitals.
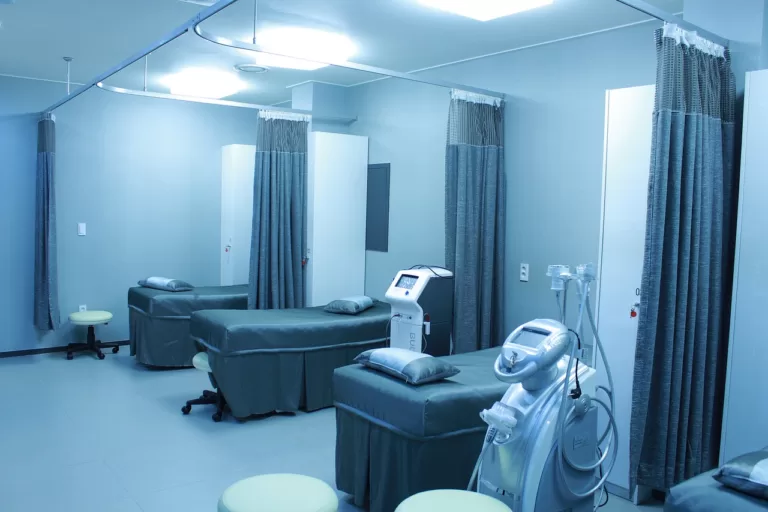
Each asset and component must be evaluated individually when determining its life cycle strategy. It’s only then you will make the best decision about which asset management life cycle strategy to follow:
1. Condition Based Monitoring & P-F Curve)
2. Design Out (Engineering design led changes)
3. Risk Based Preventive Maintenance (FMEA & FMECA)
4. Reliability Centered Maintenance (RCM)
Condition Based Monitoring & P-F Curve.
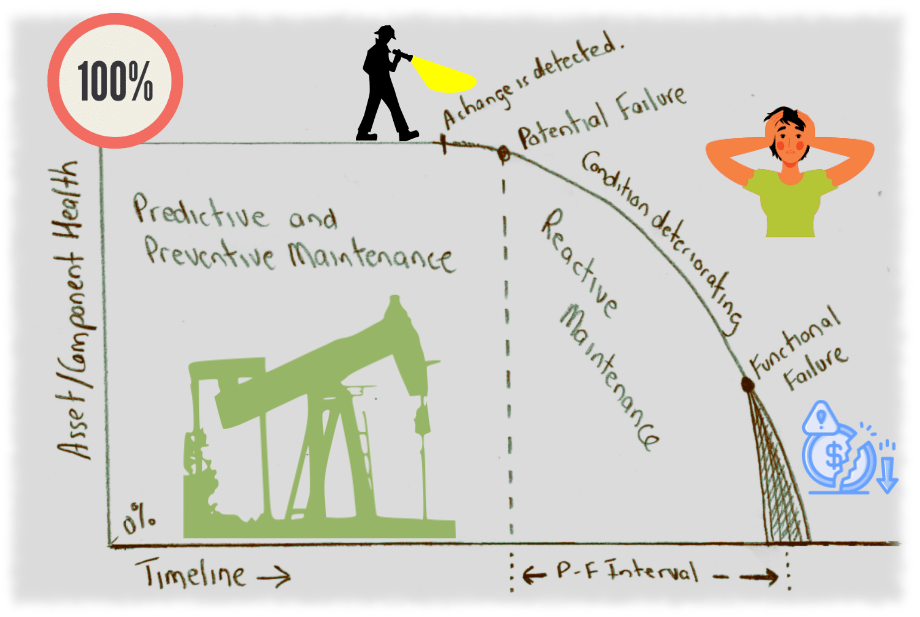
Condition-based maintenance (CBM) is based on the fact that most failures do not occur instantly but develop over time, and the P-F curve is an effective way to show the health of equipment over time.
The P-F curve graph depicts the time interval between potential failure and functional failure. The goal is to detect and respond to impending failures as soon as they are actionable. CBM entails recording specific data and measurements such as vibration, temperature, and noise to provide engineers with an indication of asset condition.
CBM does not always have to be prohibitively expensive; for example, SKF has some incredibly good and reasonably priced Condition Monitoring tools, such as contact and infrared thermometers, as well as their QuickCollect sensor.
The SKF QuickCollect sensor is a simple bluetooth-enabled handheld sensor that can be connected to your phone or tablet to display real-time temperature and vibration data. This makes it an excellent tool for conducting plant walk-around inspections.
Operators who use the same piece of equipment on a daily basis become very familiar with it and finely tuned to it. They make extensive use of their senses, especially:
1. They can frequently hear any equipment changes due to different noise levels.
2. They can feel any defects in rotating equipment via vibrations they can feel with their hands and feet.
3. They can detect any temperature changes via touch or radiated heat from equipment that starts to get a tad hot.
Although adhering to the P-F curve is the only way to do business in some cases, it is not always the best approach for every asset or component. Condition-based maintenance tasks are frequently based on the actual or perceived life of an asset or component.
This asset life is frequently many times greater than the P-F interval, and if we stick to the condition-based maintenance strategy without question, the CBM results over a few years can sometimes be less-than-ideal.
P-F curves can be used to determine asset/component replacement or overhaul activities in a very safe and critical manner. However, on reasonably similar assets, the P-F curve can result in significant length variations.
The P-F Curve indicates the time span between when potential failure is predicted and when Functional Failure is almost certain. The nature of the equipment, the availability of related spares, and other factors such as failure consequences will determine where in the P-F interval the replacement will take place.
Design Out (Engineering design led changes)

Designing your way to better results is a common method of increasing reliability and availability in newly constructed processing plants.
This method has the potential to be extremely effective, but it necessitates data collection and consultation before any significant changes are implemented.
For example, replacing an asset’s drive with a more powerful electric motor is sometimes, but not always, a good solution.
If you upgrade an electric motor due to inexcusably frequent tripping problems, only to discover later that the problems were caused by constant operator error, the design change can be costly and unwelcome in the plant.
Nothing beats conducting research prior to making major changes. A design change can be inexpensive, easy to justify, require few procedural changes, and deliver guaranteed better results in some cases.
When bottlenecks in the process are causing issues downstream and upstream of the offending assets, design changes are sometimes the only way to address recurring issues.
Risk Based Preventive Maintenance (FMEA/FMECA)
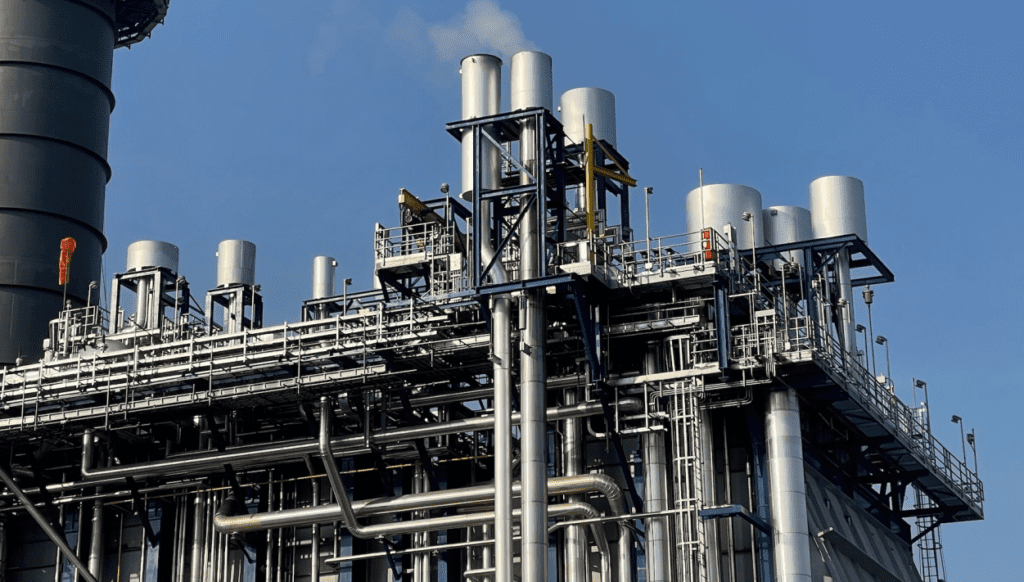
Failure Mode Effects Analysis – FMEA.
Failure Mode Effects Criticality Analysis – FMECA.
Both the FMEA and FMECA methods are very effective engineering analysis techniques that, when used correctly, can be extremely useful in assisting engineers’ decision-making processes.
Because it examines equipment and components down to the smallest spare part level, this type of analysis is often referred to as ‘from the bottom up’ analysis.
FMECA analysis entails calculating or determining the criticality of each failure mode identified.
Some common reasons for component failures.
1. Imbalance
2. Corrosion
3. Electrical Problems
4. Lubrication Contamination
5. Lack of Lubrication
6. Misalignment
7. Looseness
8. Vibration
9. Bearing Damage
10. Gear Mesh Damage
11. Fan blade Damage
12. Cracks in shafts
FMECA analysis is by far the most common type of reliability analysis that I can think of, and it has proven to be effective in almost every industry time and again.
FMECA entails taking into account every possible mode of failure of a single asset or component of a larger system. The consequences of each possible failure mode are then analysed and determined by FMECA.
When your company does not have FMECA analysis or maintenance strategy development software, FMECA spreadsheets are typically used.
When people have received FMECA training, they start thinking about:
1) What might fail?
2) How often could it fail?
3) How it will fail?
4) How badly it will fail & what’s the worst that could happen when it fails?
a. A severity rating of the consequences is assigned, a ranking from insignificant to Catastrophic.
5) The probability of each failure mode.
FMECA investigates the possibility of detecting failure modes before the consequences of failure become apparent.
FMECA is widely used in modern asset maintenance strategies and is by far the most common approach I see being used in the mining industry of late.
Flowcharts and fault-finding tables are also used as diagnostic tools.
FMECA analysis will reveal any potentially critical single-stream processes in your organisation (no process redundancy). FMECA is also used to analyse testability, especially for electronic subassemblies and components, as well as systems.
FMECA analysis can also be used to determine how well your process plant operating system can be tested, how cost-effectively it can be tested, and whether all potential failures can be identified and reported.
To specifically consider the possibility of process/production-induced failures, a FMECA analysis can be performed.
A production FMECA can be extremely useful in testing the vigor of the overall design and what can be expected in terms of ease of operation over time.
Reliability Centered Maintenance (RCM)
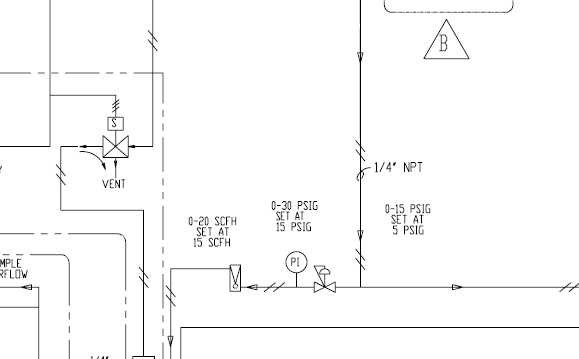
RCM is functionality based methodical approach to analysing an asset’s or system’s functions.
It investigates the potential failure modes of assets, components, or system-related functions and provides you with the priority-based safety, practicability, and financial soundness considerations needed for your assets to be as reliable and available as possible.
RCM’s primary goal is to reduce your organization’s total costs, not just maintenance costs. If we are unable to operate and maintain our assets in a financially sustainable manner that ensures our long-term viability, there are fewer and fewer reasons to stay in business.
The aspect of RCM that I like best is that it requires you to start from scratch, as if you know nothing about the equipment or components you want to analyse; this is known as a Zero-Based approach. Every process component is examined, every possible failure mode is sought, and appropriate actions are assigned.
The RCM goals typically include:
1. Improved levels of health, safety and environmental integrity.
2. Better operational performance and experience.
3. Greater overall cost effectiveness.
4. Extended the life of your assets and components.
5. An interdependent asset performance culture, improved teamwork, and increased workplace enthusiasm.
The style of RCM questions that get asked are:
1. How does the asset or component currently operate in terms of its required functions and performance standards?
a. It is essential to understand all functions of essential equipment
i. Primary Functions
ii. Secondary Functions
2. How might it be unable to carry out meet its functional requirements?
3. What is the underlying reason behind every functional failure?
4. What occurs if each functional failure materialises?
5. How might every failure be anticipated or prevented?
6. What should be done in the absence of a suitable preventive or predictive measure?
What do you hope to achieve
What motivated you to buy this asset/component in the first place?
What is your desired performance specification? Assume that any & all other factors have zero influence.
1. Output.
2. Quality.
3. Safety.
4. Efficiency.
5. Environmental sustainability.
What is the asset/component actually capable of achieving?
Are you able to operate this asset/component over 100% of the design parameters? If so, how far can you go?
Exactly how does it fail? What happens when it fails?
The underlying tone of these 2 questions is to eliminate or minimize the consequences of every failure.
You need to be able to successfully deal with any consequence that a failure might cause:
1. To itself
2. To anything physically near it
3. To anything downstream of it in the process.
4. What happens to everything upstream in the process to it.
· It is possible for things to start to overflow? The operating system logic should prevent this but has it ever been tested?
When this thing fails, does it fail in the same way that other similar equipment you’ve seen or enquired about fails?
If you are a new facility, what do you think will happen if & when this thing fails for the first time? You need to flesh out, from best to worse case scenarios and everything in between.
Is it possible that this asset or component will experience hidden failures? These situations will not be obvious; there will be no obvious symptoms in a lot of cases.
Developing an understanding of any potential hidden failures is extremely important, especially if these things are designed to protect people, processes, systems, equipment, software, or devices.
Naturally, there will be a greater emphasis on any failure that has the potential to injure or kill someone, affect the health of one or more people, or damage the environment in any way that violates your country’s environmental act.
To get RCM up and going at your workplace you will need to engage or possibly employ an RCM facilitator and begin rolling out training.
Review teams will need to be established and hopefully these can involve a wide mix of roles within the organisation. The review teams are naturally guided your RCM expert/facilitator.
[…] To expand on this info, read my latest article at: https://www.cmmssuccess.com/get-the-most-out-of-your-assets/ […]
[…] To learn more, read my latest article at: https://www.cmmssuccess.com/get-the-most-out-of-your-assets/ […]
[…] To explore this topic further, read my latest article at: https://www.cmmssuccess.com/get-the-most-out-of-your-assets/ […]
[…] For additional information, read my latest article at: https://www.cmmssuccess.com/get-the-most-out-of-your-assets/ […]
[…] To learn more, read my latest article at: https://www.cmmssuccess.com/get-the-most-out-of-your-assets/ […]
[…] Training for Planners – CMMS SUCCESS. Your boss needs solutions not problems – CMMS SUCCESS. Get the most out of your Assets – CMMS SUCCESS. Planning Maintenance Using SAP – CMMS SUCCESS. Will AI Make Asset Management Better – CMMS […]