Complete Maintenance Systems Audit – Part 2
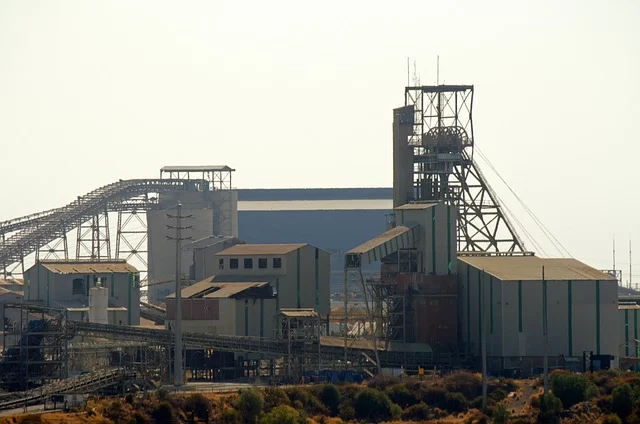
The article is intended to be read directly following Maintenance Systems Audit Part 1 (Master Data, Maintenance Strategy, Identify, Plan & Schedule Work)
Maintenance Systems Audit Module 5 – Execution Readiness.
This module is split into 3 sections:
1. Shutdown Maintenance Execution Readiness.
2. Operations Run-down & Start up plans for Shutdowns.
3. Routine Maintenance Work Execution Readiness.
Section 1 – Shutdown Maintenance Execution Readiness

12 Weeks Prior to Shutdown Event.
1. Are Shutdown Codes being used for outage events?
a. A Shutdown Code should have been assigned to all work orders intended to be carried out during the upcoming event.
i. If not, does the CMMS have the functionality?
ii. If yes, why don’t they use it? Is the functionality flawed?
2. Draft Shutdown Scope Review.
a. A draft scope of work should be reviewed at this point, is this data extracted from the CMMS via dedicated query using the shutdown code?
· If work orders are coded correctly, this data should be easy to extract.
· Is this data manually extracted via multiple data extracts and put together in a spreadsheet?
3. Set a ‘Scope Freeze Date’ and stick to it.
a. 12 Weeks prior to the Shutdown Event, a date should be nominated for freezing of the scope.
b. Is there functionality within the CMMS to ‘lock the scope’?
c. Users should either be prevented from adding to the scope of the event beyond scope freeze date.
d. If the task must happen at that time, an approved emergent work request should be used
e. Better still, if there is a process within the CMMS for approving an emergent work order with a shutdown code that is past the scope freeze date. A sub process could be initiated as soon the shutdown code is applied to a work order after the scope freeze date.
4. Materials Management – Set ‘Date Required’ for all parts.
a. Is a date set where all parts for the shutdown must be ready?
b. All parts requested via work orders that are approved for the shutdown should have the ‘date required on site’ changed to this cut of date or earlier.
c. Does the CMMS have functionality for this?
12 to 9 Weeks Prior to Shutdown Event, Draft becomes Planned
1. All work orders relating to this shutdown event must now be coded as planned.
a. Have all draft shutdown work orders been reviewed for quality and relevance and coded as ‘Planned’?
b. Check for instances of Planned shutdown work orders that have:
i. Already been completed
ii. Little to no scope of work
iii. No parts ordered
2. Assess the Shutdown Risks
a. Now that all shutdown work orders are considered to be planned for this event, all risks should be evaluated and mitigated.
b. Is there a process for assessing the risk of the shutdown work?
c. Assess the risk of the shutdown as a whole, in each production area and each work order.
3. Shutdown Work Packs
a. Is a role appointed for ensuring the quality of all shutdown work packs?
b. It may be the planner but could also be a tradesperson that does this role as a secondment.
4. The scope of the shutdown should now be locked
a. The scope of work for this shutdown even should now have been locked or frozen.
b. Is the significance of freezing the scope fully understood and embraced?
c. Are there any instances of work orders still being included into the shutdown scope regardless?
d. Is there an emergent work process and is it used?
Is requesting emergent work a manual process or is it managed through CMMS functionality?
5. Managing & Staging Shutdown Parts
a. As shutdown coded work order parts arrive on site, are they sorted by work order and are they being placed in an area dedicated for the shutdown?
b. Are these parts secured to prevent people from using them on routine work orders?
c. If there is an emergency/breakdown work order and a part dedicated for the shutdown needs to be used to keep the plant running, is there a process for immediately expediting this part?
6. Postponing of planned shutdown work orders
a. If work orders are reviewed and it’s determined that they will now be done on the next shutdown, in addition to the new code being put on the work order, is the warehouse notified that that part needs to be removed from the current staging area.
b. Is there another staging area for the shutdown following this one or will these parts get put back onto shelves?
c. If these parts were direct purchased, will they now be added to the inventory and managed via the warehouse or will they be placed into some general area?
9 to 6 Weeks Prior to the Shutdown Event, the scope is final and approved.
1. Scope Finalisation & Manager Sign Off
a. The scope should now have been finalized and signed off by the Maintenance Manager, does this take place?
b. Can you verify that Maintenance Manager sign off prevents any additional work from being added to the scope? (The emergent work process should no longer apply).
2. Is a Health, Safety & Environment Audit now conducted on all upcoming shutdown work?
3. Are work zone supervisors now appointed for the shutdown?
a. If so, all work packs should be split up per work zone supervisor.
b. Work Zone Supervisors should then be conducting a readiness audit for all work packs assigned to them. Is there functionality within the CMMS to designate work areas or zones?
4. Shutdown Gantt & Management Plan
a. Is the Shutdown Gantt Chart updated and communicated to all stakeholders (internal and external)
b. Has the Shutdown Management Plan been finalized and communicated to all stakeholders (Internal and External)
6 to 3 Weeks Prior to the Shutdown Event, all resources for the event should now be locked in.
1. All names (internal and external) for this shutdown event should be locked in and any medicals, inductions etc should all be in the process of being carried out, is there progress reporting on all these tasks?
2. There should be an array of audits happening on site during this time, lift audits, fire protection audits, facilities/amenities audits etc, are there work orders for all of these tasks?
3. If this site is a remote location, by now all additional accommodation requirements should have been finalized and any additional accommodation dongas should have been set-up and all services connected etc, is there progress reporting on these actions?
4. If this site is near a town or city, are all motel rooms, rental accommodation, caravan park accommodation etc now all be confirmed for any external resources? Is progress reported?
5. All names of people ‘locked in’ to be performing the work should now be added to the Shutdown Gantt Chart?
6. Has this information been communicated to all stakeholders (internal and external)?
7. Has a site layout plan been sent to all external companies?
8. The cut-off date for all parts arrivals should now have been reached.
a. Were there many parts that did not arrive in time?
b. Is the situation of not having these particular parts risk assessed?
c. Has a lay-down area been prepared for parts adjacent to the plant?
d. Are all parts not requiring special storage instructions now being transferred to a dedicated area?
9. Isolation Plan & Work Permits
a. All isolation plans and permit forms should now have been completed?
b. Have Isolation officers for the shutdown been appointed?
3 to 0 Weeks Prior to the Shutdown, final preparations are now complete.
1. Has shutdown preparation activity reduced dramatically, by now there should be only a few tasks being sorted out?
2. Has all scaffolding been erected and inspected for safety compliance?
3. Is all additional machinery onsite by now?
a. Generator Sets for power outages, bobcats/skid steer loaders, additional hire utes should be on site and have been inspected for site compliance.
b. Have buses been organized to transport people to and from site? Telescopic Handlers, Forklifts.
4. Has a grid-mesh audit been conducted by now?
a. Any repairs/replacement should be completed by now.
5. Are all external company representatives coming out to site prior to the shutdown event and familiarizing themselves with the work?
6. Are all work packs complete and ready to be handed out?
7. Have additional skip bins been organized for waste and recycling etc?
8. Has the ‘Post Shutdown’ process been finalized and distributed to all stakeholders?
9. Have the work orders been changing in status during the phases of readiness for the Shutdown Event?
Section 2 - Operations Run down & Start up Plans for Shutdowns
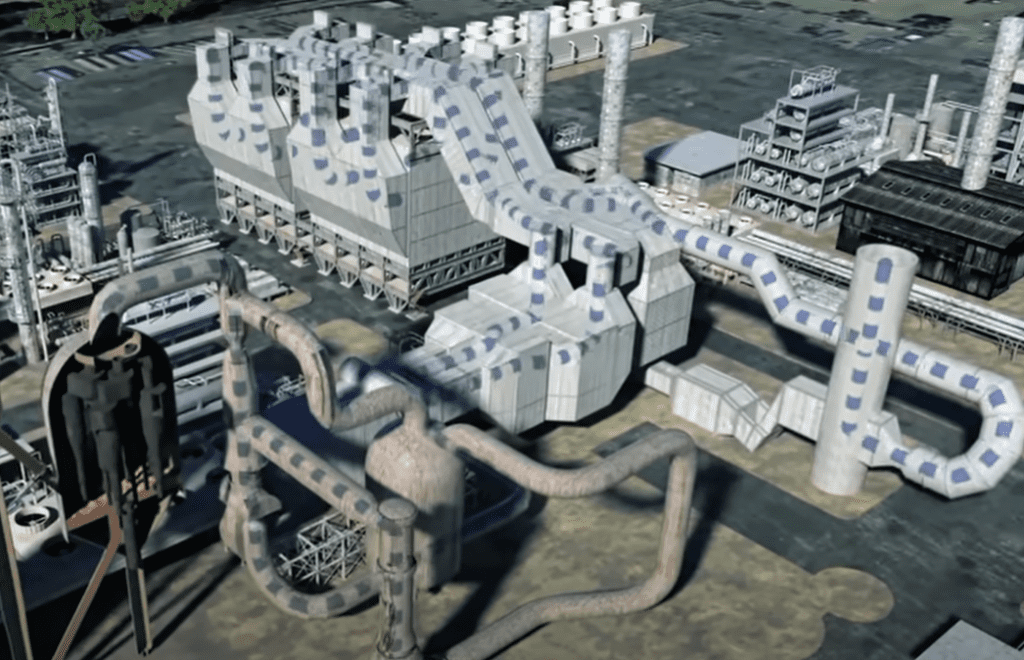
Operations Run down plan
Preparing the plant for the shutdown maintenance.
1. Did Maintenance & Operations personnel work together in producing the ‘Run down plan’?
2. Was the ‘Run down plan’ produced in Gantt chart format, the same as the Shutdown Schedule?
3. As ‘Run down plans’ will allow certain production areas of the plant to be available to maintenance earlier than others, have milestone tasks been identified to allow maintenance execution tasks to be linked?
a. This is referring to ‘Finish>Start’ relationships. The finish time of each ‘Run down plan’ milestone should be linked to the start time of the first maintenance task for that area.
4. Was the ‘Run down plan’ approved by both the Maintenance & Production Mangers?
5. Was the approved ‘Run down plan’ included at the beginning of the Shutdown Schedule?
6. Have maintenance & operations personnel been assigned to every task of the ‘Run down plan’?
Operations Start up plan
Energizing the plant with all services & feed – Establish steady state running
1. Did Maintenance & Operations personnel work together in producing the ‘Start up plan’?
2. Was the ‘Start up plan’ produced in the same format of Gantt chart as the Shutdown Schedule?
3. As ‘Start up plans’ will need certain production areas of the plant to be available for processing earlier than others, has the Shutdown Schedule been altered to accommodate these requirements?
4. Have milestones been created in the Shutdown Schedule for the last maintenance tasks that affect the operational start up for each production area?
5. Have these milestones been linked to the first task of the Operations Start up plan? This is referring to ‘Finish>Start’ relationships. The finish time of each ‘Shutdown Schedule’ milestone should be linked to the start time of the first Operational start up task for each production area.
6. Was the ‘Start up plan’ approved by both the Maintenance & Production Mangers?
7. Was the approved ‘Start up plan’ included at the end of the Shutdown Schedule?
8. Have maintenance & operations personnel been assigned to every task of the ‘Start up plan? Have additional Maintenance Resources been organized to be a part of the production crew for the first few hours post shutdown?
Section 3 – Routine Maintenance – Typical Work Execution Readiness
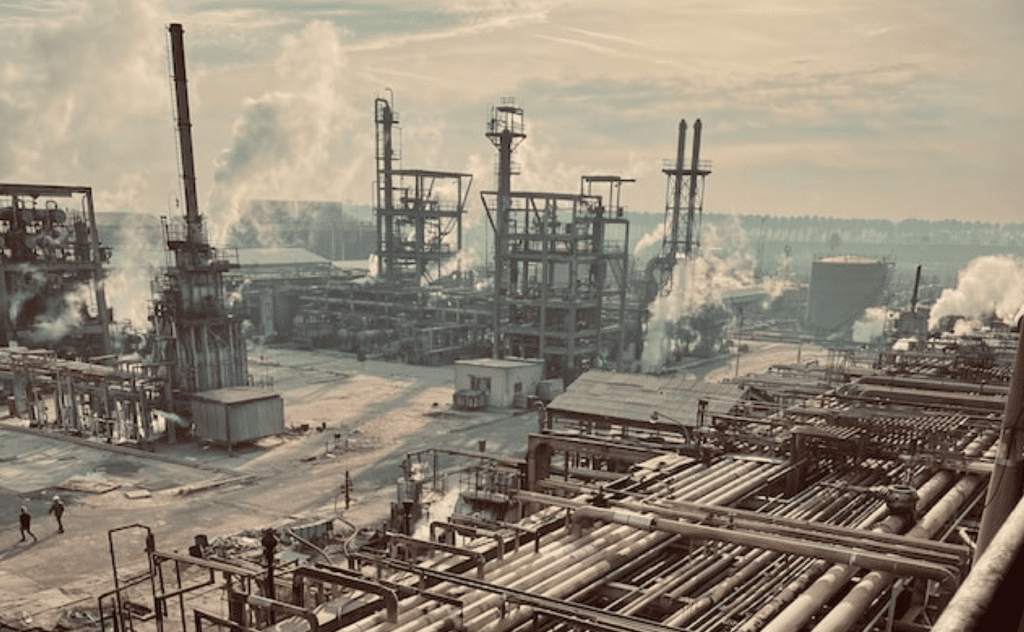
1. Are all work orders for the upcoming execution period coded uniquely?
2. Does the supply department assign a person to manage expediting and organizing of all parts for the upcoming execution period?
3. Does the warehousing function stage all parts assigned to the code for the upcoming execution period? Are there regular parts status reports being sent to the maintenance people?
4. Is there standard CMMS functionality for the maintenance people to view the parts status information live?
5. Is there a cut-off date for all parts arrivals for upcoming execution period based on the proximity to the earliest start date, e.g. 1-2 weeks prior to the earliest start date?
6. Are all contract resources, support equipment, access equipment and any other external requirements identified and managed via work orders?
7. Is there a process for ensuring that all external requirements are on site and fit for use at least a few days prior to start of the execution period?
8. Are all names (internal & external) finalized for the upcoming execution period at least 1 week prior?
9. Are these people provided with a list of work orders that they will be tasked with performing prior to that period?
10. Is there evidence of people reviewing their assigned work in advance and making comments about work order readiness?
11. Is the scope for the upcoming execution period ‘locked’ or ‘frozen’ at least 1 week prior?
12. Is there a CMMS status for work orders being 100% ready for execution?
13. Are all repairable and rotatable parts identified?
14. Are all these parts checked for quality prior to use?
15. Is there a site process for returning these parts back to the store in the correct condition (void of any fluids and cleaned etc)?
16. Are work packs developed for the more complex maintenance tasks?
[…] Maintenance Systems Audit Part 2 (Work Execution Readiness) […]
[…] Maintenance Systems Audit Part 2 (Work Execution Readiness) […]
[…] Maintenance Systems Audit Part 2 (Work Execution Readiness) […]
[…] This article should be read in conjunction with Maintenance Systems Audit Part 2 – Module 5 – Execution […]