Steps for Ensuring CMMS Quality Work Orders
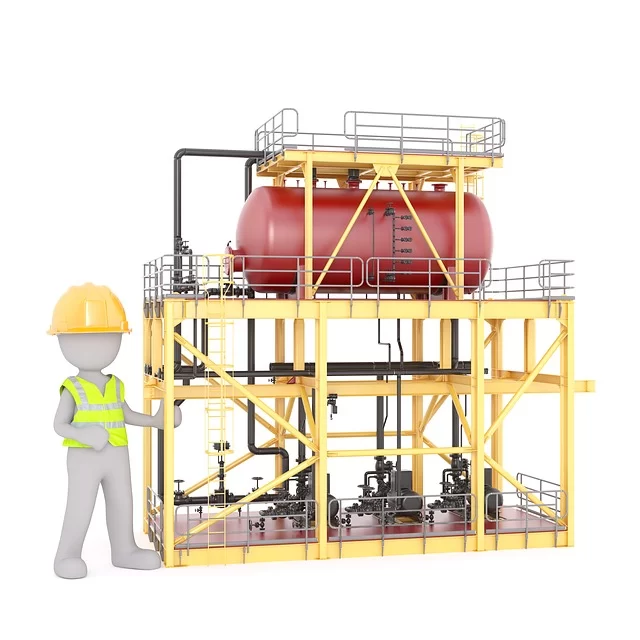
Work Order Quality Requirements
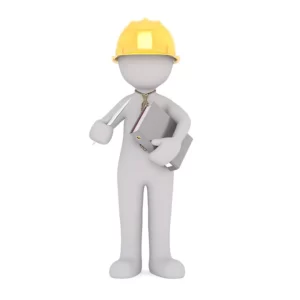
Once any new work requests have been reviewed and approved, it is up to the Maintenance Planner to compile all of the necessary information in an approved quality format so that the maintenance execution team can carry out their work in the safest, efficient, and effective manner.
If a Work Order contains multiple tasks, these tasks must be completed in a specific logical order. Your CMMS should have the functionality to apply task dependencies or relationships to ensure that task sequencing, once set-up, cannot be undone.
To ensure accurate start to finish durations of work orders, make sure all tasks have all trade types identified and that each trade has been allow sufficient time to complete their work safely and in full.
If you take the time and effort to create work orders with the appropriate number of tasks, task dependencies, and related hours, you can provide the operations department with quality asset handover information to organise themselves around.
Work Orders that involve rectifying defects
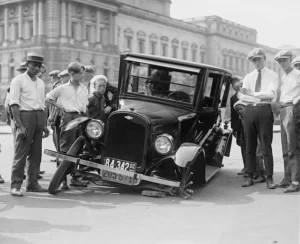
Defect rectification or Corrective Maintenance work orders have a higher risk of planning errors than maintenance strategy work orders. Strategy work is typically put together by engineers using risk based, failure mode specific reliability methodologies, and as such tend to have everything accurately identified and thoroughly planned.
The risk of a maintenance strategy work order failing to clearly identify all risks and required actions is low.
Strategy work focuses on preventing problems from occurring, whereas corrective work is used to address a problem that has already occurred or about to occur.
Unless Corrective Maintenance is thoroughly planned and implemented effectively, there is a good chance you will hear about how that asset failed in the near future, costing the company a lot of money to replace or repair in an emergency response situation. There are far too many cases where reviews of emergency/breakdown work reveal one or more simple but critical planning steps that were either not thought of and planned or were planned but not carried out.
With this in mind, your CMMS should include a risk assessment method for corrective maintenance work that assigns a priority, as well as an engineering review and approval workflow method for corrective work orders that are at a certain level of risk. It is far better to add an extra step or two to the work order planning process than to put your company at risk of production losses.
Plan what needs to be done before the maintenance work
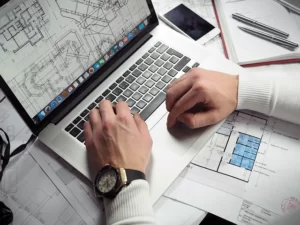
For any intrusive or complex maintenance work, creating a Pre-work section of the work order can be extremely beneficial. The goal of the pre-work section is to identify any Job Preparation, Health, Safety, and Environmental issues related to maintenance work, as well as any requirements to address those issues.
This section’s issues and requirements should be clearly related to any work order tasks that have been created; the more task specific this information is, the more useful it will be to the Technician. Assuming that Technicians are given enough time to act on this information, it can ensure that they arrive at the job site on the scheduled day for this work with everything they need and no reason to delay starting the work.
Check all the parts prior to use
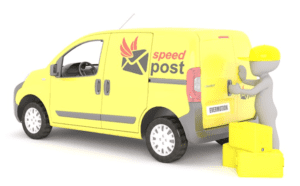
Nothing irritates Maintenance Managers more than seeing technicians standing around at the warehouse when they are supposed to be performing maintenance work because of:
1. They have had to return incorrect parts
2. They are waiting to be issued parts that were not identified for the job
3. The part that was issued to the job is faulty or damaged
4. There was not enough of the correct parts issued to the job
There’s no real point for the Maintenance Manager to ask any questions about how these situations can possible exist, they already know the answer. The parts requirements were not checked prior to the work commencing.
Part of the Pre-Work section must include reviewing all parts assigned to maintenance jobs sufficiently prior to the job’s start date, so that if the warehouse does not have stock of an additional or defective item identified, the purchasing team has enough time to expedite delivery.
Effective use of Critical Contract Resources
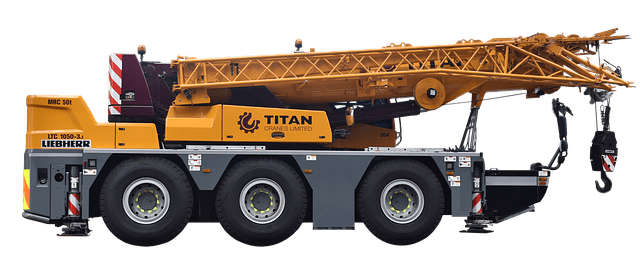
It is critical that any work order tasks that require the use of equipment access services/equipment or material handling/lift and shift equipment receive extra planning attention. This work may include scaffold erection, the delivery of EWPs/Scissor lifts, and the use of lift and shift equipment (Forklifts, Telescopic Handlers or Cranes).
This section might include lift studies being carried out by the Crane Company and checking the suitability of any scaffold that has been built so far.
Handing over equipment to the Production team.
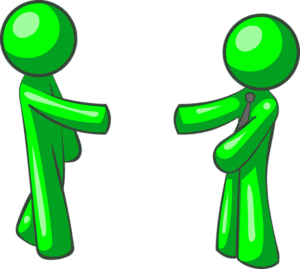
If work orders are risk assessed at a certain level, a section within the work order should clearly define the process of inspecting, testing, and handing over fit-for-purpose equipment to the production team.
This procedure may also include putting certain equipment or personnel on standby during the startup process and for a period of time afterwards to ensure that any risks identified can be quickly and effectively addressed with minimal production loss.
Identify & Perform Inspections & Tests prior to Handover.
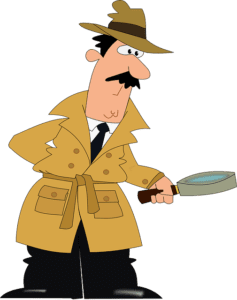
If the scope of the maintenance work to be performed involves tasks that are:
1. At risk of failing at start up or soon after
2. Would be difficult or unsafe to examine once the plant is running
3. Involving welding of exotic alloys (hastelloy, duplex, titanium etc) via TIG, MIG or plasma arc welding
The work must then be inspected and tested by qualified personnel before being handed over to production and adequate time should be allowed for this in the work order’s handover section.
Reviewing work order quality and costs
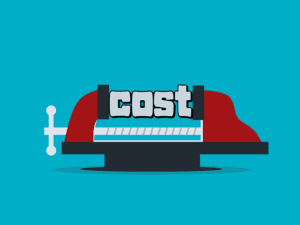
After completion, any completed work with a high risk level, complexity, or significant estimated cost should be reviewed to look for opportunities to improve in the future.
This is especially true if the work is new to your company and was planned from the ground up. Everything learned from this work should be reviewed, and the approved outcomes should be used to create a work order template that can be used again and again.
If your company develops a habit of doing this, you will end up with a very accurate estimating index on site, which will be extremely useful when compiling your yearly budgets.
Technician Feedback to Planners and Engineers.

Technicians should be encouraged to provide feedback and markups on work orders in order to identify and address any errors, deficiencies, or other issues with work order tasks and related scopes of work. The maintenance supervisor should review this information before passing it on to the planners or engineers.
If the Technician feedback on a work order necessitates the creation or modification of your maintenance strategy, this should be initiated and actioned via the technical or engineering change management system.
Technicians should also provide feedback on spare part issues. If they have suggestions for better or different parts and can provide some details on the current problem, what impact it is having, what their solution is, and how long before the company should implement the change, this information can be processed through the technical or engineering change management system.
Within the warehouse, spare parts management should include in-store maintenance of repairable items as well as planned period testing and inspection of critical items. This should almost certainly include the use of Positive Material Identification devices, such as the Bruker S1 Titan Analyzer, to verify the alloy grades of critical parts. In certain plant environments, incorrect material usage can have disastrous consequences.
The Bruker model mentioned is what’s called a X-ray Fluorescence Analyser. They are very lightweight, not more than 1.kg with the battery plugged in and are connectable via wifi or usb. this is the link if you would like to learn more.
All specifications for any spare parts that have been catalogued, as well as storage and handling instructions, should be included in the Material Master File. If your CMMS currently does not allow for the entry of that data, you should look into it. Instructions for storage and handling can range from simple statements like “store on a hard flat surface” to more complex statements like “store in a temperature and moisture controlled environment, maximum temperature 32 degrees Celsius, less than 70% humidity.”
Whereas I might always push to get the functionality within your own CMMS, there another option for linking all information you might want to know about a part to its master file. The software product is called Linkone and you can go much further than just linking some specs and comments. You can link drawings, videos, animations and any documents you might have, this is the link if you’d like to learn more.
[…] status. If you’d like a look at what I feel a fully planned work order looks like, here is an article I published on my Blog Page about this subject a while […]