Complete Maintenance Systems Audit – Part 3a
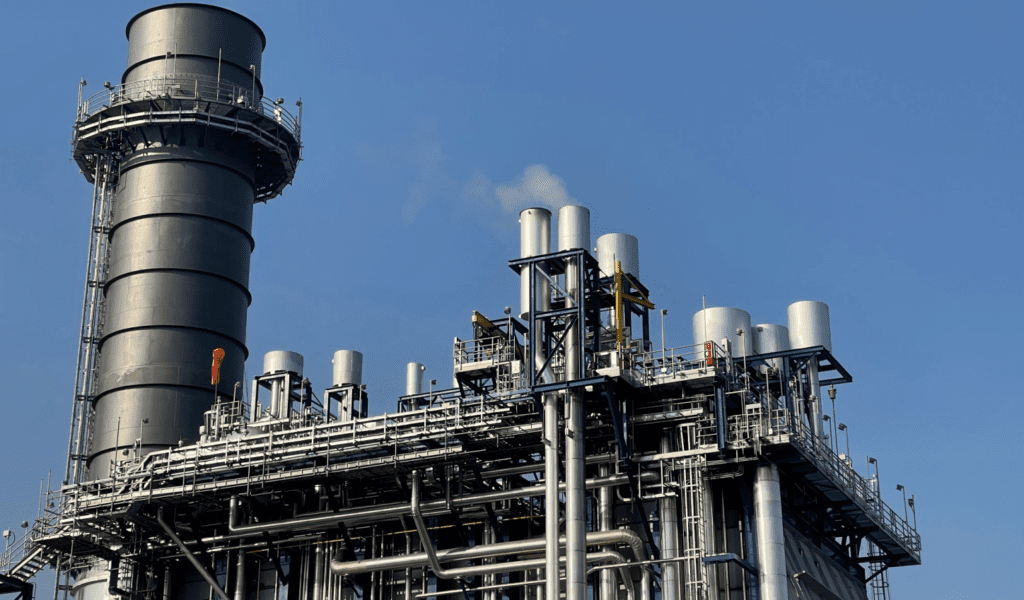
The article is intended to be read in association with:
Maintenance Systems Audit Part 1 (Master Data, Maintenance Strategy, Identify, Plan & Schedule Work)
Maintenance Systems Audit Part 2 (Work Execution Readiness)
This article details Module 6 – Section 1 – Execute Work – Shutdown Maintenance.
Work on assets during shutdown environments and other major maintenance events consume a significant portion of maintenance budgets.
If these events are not planned and scheduled with the utmost care, they can be ineffective and have a significant negative impact on both your company’s production capacity and cash flow. Shutdowns exist to complete tasks that cannot be completed while the plant is “running.” Typically, the cost of the maintenance work pales in comparison to the cost of lost production from the start to finish of the shutdown events. Maintenance departments should hire additional help to plan the work if necessary, as it is almost always worthwhile. Maintenance budgets should include ample funding for shutdown planning.
Execute Work – Shutdown Maintenance
1. Were personnel organized to come in early to make sure:
a. All crib rooms are clean and adequately prepared?
b. Wash rooms and toilets (fixed and temporary) are in good order?
c. Water bottles have been distributed evenly around the plant crib rooms?
d. All hand held radios were accounted for and found to be in their chargers?
e. All First Aid Kits are still full and in the correct locations?
f. All Utes, support vehicles and other engine driven equipment are fully fueled and fit for use?
g. Work sites were properly cleaned? Ground floor of plant was cleaned of all product?
2. Did the Operations Run down plan go according to plan?
3. Did the Shutdown Pre-Start Meeting commence on time? Did this Meeting finish within 10 minutes of the planned time? If not, did it affect the start time of the tool time for Shutdown?
4. Were any hazards discussed during the pre-start meeting?
5. Were all the required resources on-site and fit for work?
6. Did all workers know who their work area supervisor was?
7. Was all the pre-shut preparation work completed?
8. Were there many instances of employees complaining that not all parts for their specific job were available?
9. Were the trade type and hours allocations on the work orders accurate?
10. Was the scope of work on the work orders accurate?
11. Were there any hazards identified in the first hour of the shutdown?
12. Were all electrical disconnections & re-connections identified on the Gantt chart and on the work orders?
13. Were there any instances of chemicals being used during the shutdown without prior approval and/or without a MSDS?
14. Was there a work order to check all lifting gear prior to the shutdown?
15. Were task observations/safety interactions being done during the course of the shutdown?
16. Was there adequate lighting made available on the night shifts?
17. Was there enough permit offices around the site to prevent unnecessary delays to the start of maintenance work?
18. Were people challenging permit issuers to ‘test for dead’ prior to accepting permit?
19. Was there enough special tooling?
20. Was there a lot of lost time waiting for cranes?
21. Did contractors feel that there was enough supervisory assistance from site?
22. Was there much additional work during the shutdown? Could this work have been identified pre-shut?
23. Was the shutdown work completed in each area at or before the correct times?
24. Maintenance handover to production was done as per plan for all areas?
Points to consider when evaluating the overall effectiveness of a shutdown.
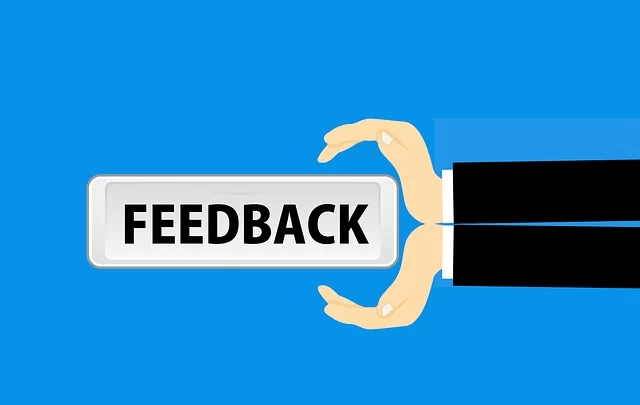
It is critical for effective shutdowns to maximise
the quality of planning prior to the event, and engineering staff should be
involved at key junctions to ensure acceptable risk profiles and the complexity
of the work to be done during the event.
For reasons that could have easily been addressed
prior to the shutdown, far too much maintenance work frequently goes unfinished
and is pushed back to the next shutdown. The greater the number of times
shutdown work is postponed, the greater the risk of production losses due to
equipment failure. Furthermore, as shutdowns fill up with jobs that have been
postponed multiple times, maintenance personnel will feel pressure to complete
this work and may take risks that they would not consider in normal
circumstances. Before considering postponing any shutdown job that could not be
completed on the first attempt, a 5-Whys analysis should be performed. You are
simply postponing the problem if you do not do this.
When you cram a shutdown full of jobs that you’ve
consistently been unable to complete in previous events, you’re setting
yourself up for failure. Don’t do it. There is no shutdown job that is so
critical that it cannot be completed safely, so maintainers must be very
descriptive in their comments/feedback to supervisors about why a job could not
be completed, and those individuals should be involved in the post-shutdown
review of that job.
[…] Maintenance Systems Audit Part 3a (Execute Work – Shutdown Maintenance) […]
[…] Maintenance Systems Audit Part 3a (Execute Work – Shutdown Maintenance) […]