Complete Maintenance Systems Audit – Part 4
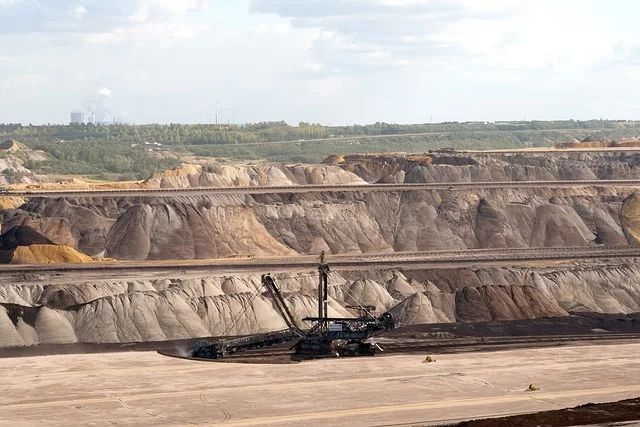
The article is intended to be read in association with:
Maintenance Systems Audit Part 1 (Master Data, Maintenance Strategy, Identify, Plan & Schedule Work)
Maintenance Systems Audit Part 2 (Work Execution Readiness)
Maintenance Systems Audit Part 3a (Execute Work – Shutdown Maintenance)
Maintenance Systems Audit Part 3b (Execute & Complete Routine Maintenance)
This article details:
· Module 8 – Maintenance Systems Management & Compliance.
· Module 9 – Improvements.
· Module 10 – Managing Costs & Reporting Functions.
Section 1 – Maintenance Systems Management & Compliance

1. Is there a periodic Maintenance Management Systems governance meeting?
2. Are there role based business processes?
3. Have all assets been assessed for business criticality? Is there a code for criticality applied to asset numbers in the asset hierarchy of the CMMS?
4. Are all Key Performance Indicators (KPI’s) available on the company intranet? This might be in the form of a Dashboard or a SharePoint Page.
5. Indicate if these metrics are measured:
a. % Schedule Loading (Hours) – – Target V’s Actual
b. % Schedule Compliance (Count of Work Order Tasks) – Target V’s Actual
c. % Schedule Work (Hours) – Target V’s Actual
d. % Planning Accuracy (Hours) – Target V’s Actual
e. % Availability – Target V’s Actual
f. % Reliability – Target V’s Actual (There might be MTBF targets for differing Machinery Types)
g. % Utilization – Target V’s Actual
6. Are explanations of how each KPI is developed (what data is used and how) available? Team Leaders must understand this information so that they can perform periodic self auditing of data originating from their area to ensure their staff is using the CMMS correctly.
7. Is there a Work Management Process Model?
8. Area problem solving &/or effectiveness evaluation tools used? Look for things like, 5Whys Analysis, brainstorming sessions, SWOT, ADRI. Do personnel know about the 4 types of questions? (Open, Closed, Searching, Leading), searching questions should be promoted.
9. Is there a set of metrics developed to determine if the maintenance strategy is working? When new strategies are created or when existing strategies are optimized, there needs to be ways of determining their performance, if strategies are working, there should be signs of:
a. The strategy work is being completed with little to no delay (Date Created to Complete, Date Work Order Released to Complete). If it takes too long to complete the strategy work, the right amount of work is not being done at the right time, and the plan/schedule is not being followed.
b. The strategy work order costs and hours are very close to budget. If there are unusual variances with these costs, it could be that there have been recent changes to the strategy, the strategy work is not getting done or perhaps these work orders are being used to carry out opportunity corrective maintenance.
c. Defects are being identified by maintainers during inspection work orders
d. Breakdowns are becoming less of a problem
e. Minimal Spare Parts Issues – Maintainers not needing to add parts to proactive work orders, parts allocated to proactive work orders are not being returned to the warehouse.
f. Corrective maintenance costs are on the way down. If there are unusual variances with the corrective maintenance costs, is due to inadequate planning or ineffective strategy?
· Large amounts of spare parts or labour hours being added to work orders by the execution team after they were initially released?
· Does the execution team need to organize large amounts of contract labour during each schedule execution period to make sure the work gets done?
· It might be that the maintenance strategy has not identified all of the possible failure modes. Check for breakdowns on equipment whereby there are strategies in place.
· Are most of the strategies on fixed time cycles (every 3 months etc), there can be waste with these types of strategies where they are too frequently created and if they are not frequent enough, you may not be doing the checks in time to prevent failures. Look for opportunities to change to statistics based strategies, such as every 3,000hrs etc.
· Are there a lot of instances of zero actual costs against completed scheduled work orders? This would indicate that the work is not being done (check for large amounts of break-in work). It could also mean that the equipment is not being made available to maintenance.
Section 2 – Improvements
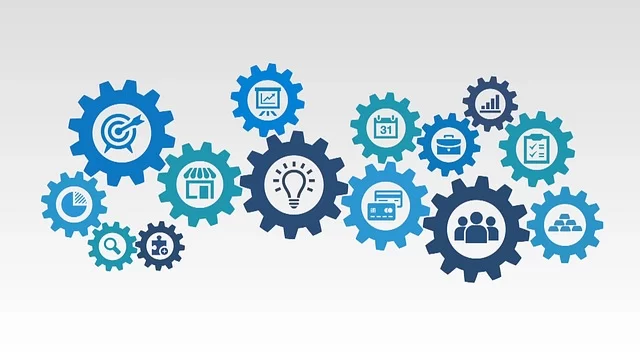
Any work required or desired that is not related to keeping existing equipment in its current state, preventing failure or decline, or repairing existing deterioration/defects is most likely an improvement of some kind.
There should be no improvement work done without the involvement of an engineer and a risk assessment by the engineering group.
Aside from being unbudgeted, improvement work can include material specification changes, make/model changes due to performance upgrades, and low-cost engineering fabrication and installation work, to name a few examples. Any type of improvement and/or engineering change carries inherent risks, and all risks in the workplace must be managed safely, legally, cost effectively & without detriment to production.
No matter how minor an improvement task may appear to you, your supervisor, superintendent, or manager, the importance of an evaluation by at least one suitable discipline engineer should never be overlooked or circumvented.
1. Is there a dedicated system within the CMMS for managing improvements &/or engineering change?
Section 3 – Managing Costs & Reporting Functions
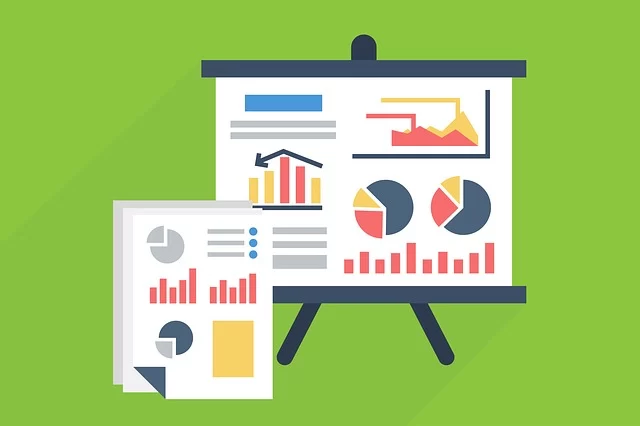
1. How effective is the managed inventory?
a. Is there a lot of direct purchasing taking place to source spare parts?
b. Are periodic audits being done on the inventory to identify if incorrect items have been obtained? These situations could be expensive to the business if there was a breakdown, the part required is booked out, only for the maintainer to find that it is not the correct part.
c. Are 3rd party companies utilized to perform inventory audits occasionally?
2. Are rotable and/or repairable spares identified and a sub system within the CMMS handles these situations?
3. Are material availability reports run on a regular basis? Are there dedicated people within the supply department expediting ‘at risk’ items that threaten having all parts needed for the upcoming execution schedule on site in time.
4. Have datasheets been created for Critical Spare Parts?
5. Are warranty periods being used effectively?
a. Are warranty profiles being created within the CMMS? Is there a unique code against an asset number that is under warranty?
b. Are claims being made during these periods? If not, there might still be potential to reclaim costs attributed to failures. Are warranty claims being tracked via reports?
c. Is there a report setup to view the status of all equipment under warranty?
d. Is there an inspection work order created to thoroughly check any equipment that will soon be out of warranty?
6. Are important parts such as insurance spares being removed from the warehouse and disposed of due to them being identified as slow moving & potentially obsolete? If so, this could be putting the company at great risk financially, these parts should be coded according to their business priority and no usage algorithm should be reviewing these spare parts.
7. Is there a process for stock preservation?
a. Evidence of this would include maintenance strategy tasks being carried out on Warehouse items. These tasks would target preventing deterioration of critical repairable parts. This might include for activities such as corrosion control, lubrication & rotating gearboxes.
8. Have bills of materials been developed for all of the most critical assets?
9. Are Manufacturing Data Records & associated material certifications being provided for any fabricated items and assemblies?
10. Is there some form of electronic shift handover between crews? Important notes relating to tasks that are not complete and to be pushed onto upcoming shift, labour issues. Good communication between shifts minimizes waste and improves ability to complete the schedule in full and on time.
11. Is there a learning management system within the CMMS? Are acquired skills categorized and included against personnel profiles? Is this information searchable for assigning correct resources to work orders?
12. Are direct purchases monitored on a regular basis? There will be opportunities within this data to catalogue parts and include them to the managed inventory. Cataloguing parts ensures parts accuracy and quality. Where companies are multi-site, catalogued parts can be visible across sites and urgent site transfers can be carried out to prevent production interruptions. Purchase agreements with vendors can be established for parts that are required on multiple sites, ensuring better price arrangements and availability.